미래차 전진기지 HMGICS
다품종 소량생산 ‘셀 시스템’ 도입
자율주행 운송에 ‘로봇 개’가 점검
가상공간 쌍둥이 공장과 동기화도
다품종 소량생산 ‘셀 시스템’ 도입
자율주행 운송에 ‘로봇 개’가 점검
가상공간 쌍둥이 공장과 동기화도
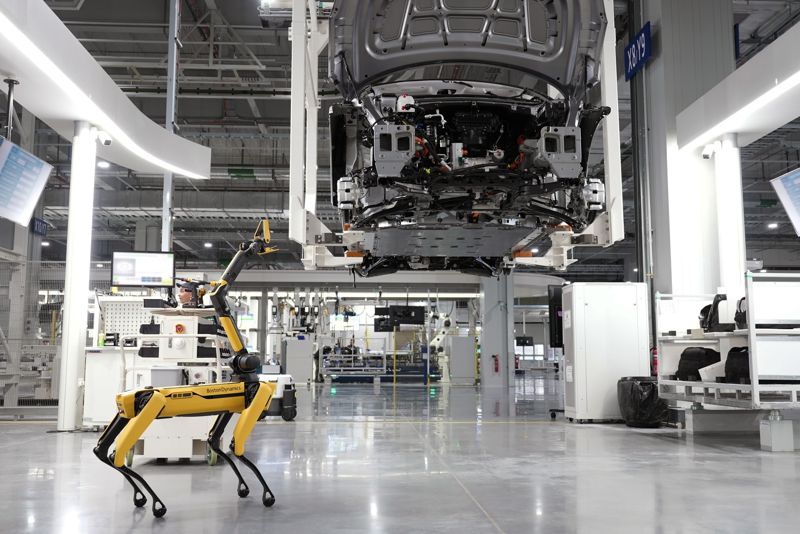
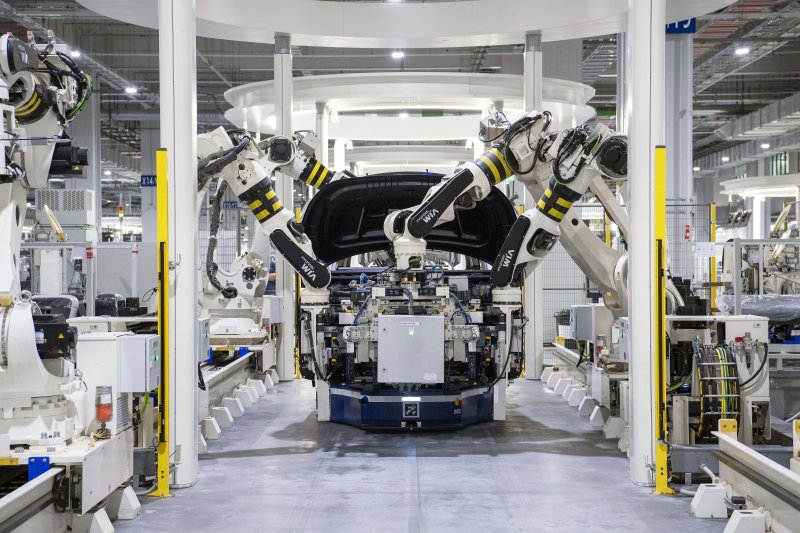
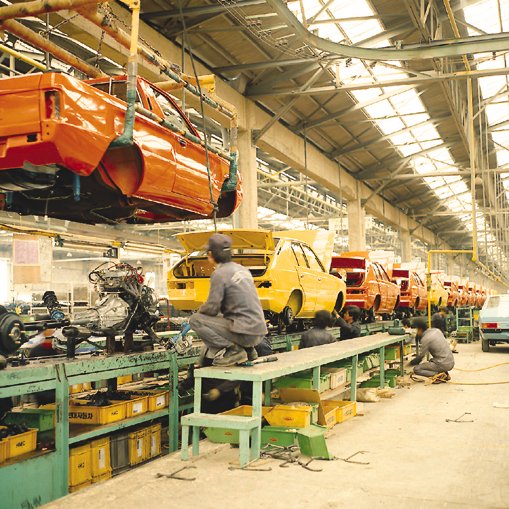
자동차 공장의 상징인 컨베이어벨트도 HMGICS에서는 찾아볼 수 없었다. 다품종 소량생산을 위해 셀 기반 유연생산 시스템을 도입했기 때문이다. 물류차 대신 자율주행로봇이 차체 부품을 운송하고 보스턴 다이내믹스의 로봇개 '스팟'이 차량 조립상태를 점검하는 스마트팩토리가 바로 HMGICS다.
정홍범 HMGICS 법인장(전무)은 "HMGICS는 현대차의 미래 모빌리티로 진행 과정의 시작점이라고 할 수 있다"며 "단순히 제조만이 아니라 다양한 모빌리티에 대해 실증을 하고 기술을 확보해 글로벌 시장에 전개할 것"이라고 말했다.
■'컨베이어' 대신 셀 생산체계 구축
전통적인 자동차 공장의 경우 컨베이어벨트로 각 공정이 연결된다. 하지만 HMGICS에선 컨베이어벨트를 찾아볼 수 없다. 대신 물류로봇(AMR)이 공장 곳곳을 누빈다. AMR은 레이더·라이다 등이 탑재돼 자율주행이 가능하며 '디지털 트윈' 기술과 연결돼 최적의 동선을 찾아 이동한다.
현대차 울산공장은 마지막 조립공정에선 일렬로 쭉 이어진 컨베이어벨트를 따라 작업자들이 분주하게 움직였지만 HMGICS에선 어떤 공정에서도 컨베이어벨트가 없다. 현대차그룹은 셀 시스템을 도입했다. 컨베이어벨트 방식만큼 단시간 내에 많은 차량을 생산하지는 못하지만 셀 시스템은 다품종 소량생산에는 최적화돼 있다. 사람과 생산 로봇이 타원형 모양의 셀 하나에서 다양한 차량수요에 맞춰 차량을 만들고, 생산하는 차종이 많아지더라도 최적화된 알고리즘으로 생산계획과 소요시간을 단축시키는 형태다.
정 전무는 "100년 동안 이어져온 지금의 방식인 컨베이어벨트로는 커스터마이징을 할 수 있는가, 그리고 누가 대응할 수 있을까 하는 부분들을 HMGICS가 생각하고 고민한 결과"라고 했다. HMGICS는 현재 아이오닉5를 만들고 있는데 연간 생산능력은 3만대다. 다만 필요에 따라선 연 5만대까지는 증산할 수 있는 시스템을 갖췄다.
■공장 내 로봇만 200대
HMGICS가 기존 공장과 또 다른 점은 사람보다 로봇이 더 많이 보인다는 것이다. 실제 HMGICS에는 총 200여대의 로봇이 운영되고 있다. 기존 자동차 공장도 차체나 도장 등에서는 자동화율이 높지만 물류나 조립공정의 경우 대부분 수작업으로 진행되기 때문에 근무인력이 상당히 많은 편이다. 하지만 HMGICS의 경우 로봇을 통해 물류는 65%, 조립은 46%까지 자동화를 달성했다. 조립 자동화율 46%는 미국 테슬라를 넘어선 세계 최고 수준이다. 궁극적인 목표는 자동화 공장을 넘어 자율 공장으로 나아가는 것이다.
정 전무는 "HMGICS는 자율 공장을 지향한다"며 "5레벨이 되면 생산 시스템 내에서 데이터를 확보하고 분석해 문제가 생기면 대책을 세워서 자율적으로 조치를 할 수 있다"고 설명했다.
또 다른 셀에 들어서자 1명의 작업자와 로봇 개 스팟을 만날 수 있었다. 스팟은 작업자를 따라다니며 작업의 완료 여부를 하나씩 검사했다. 스팟은 한번에 15장의 사진을 찍고, 이를 인공지능(AI) 모델에 전송한다. AI는 38개 파트에 대한 검사를 진행하고 작업자는 피드백을 받아 현장에서 바로 수정하는 구조다.
현대차그룹 관계자는 "인간과 로봇이 조화를 이루는 인간 중심의 제조공정 등을 통해 다양한 환경변화와 고객 니즈에 민첩하게 대응할 수 있는 환경을 구축했다"고 강조했다.
HMGICS에는 디지털 트윈 기술도 적용돼 있다. 이를 토대로 물리적인 공장 외에 가상공간에도 똑같은 쌍둥이 공장을 만들었다. 지금은 물리 공장을 가상공간에 복제하는 형태지만 앞으로는 가상공간에서 지시하면 실제 공장의 공정이 바뀌는 수준으로 동기화를 높일 방침이다. 디지털 트윈 기술을 활용하면 실제 공정을 시범가동하지 않고도 최적화된 가동률을 산정할 수 있게 된다.
현대차그룹은 HMGICS에서 개발하고 실증한 제조 플랫폼을 확산시킬 방침이다. 미국 조지아주에 짓고 있는 전기차 전용공장과 현대차 울산 EV 전용공장, 기아 화성 목적기반모빌리티(PBV) 공장 등에도 단계적으로 신기술을 도입할 방침이다.
cjk@fnnews.com 최종근 기자
※ 저작권자 ⓒ 파이낸셜뉴스, 무단전재-재배포 금지